La dureté est la qualité d’un matériau pour résister à une déformation localisée. Cela peut être particulièrement important lors de la recherche d’un matériau adapté à un environnement comprenant de petites particules pouvant induire une usure du matériau. Les matériaux mous souffrent d’indentations tandis que les matériaux durs résistent à tout changement de forme.
La dureté doit être considérée en contexte avec d’autres propriétés du matériau telles que la résistance, l’élasticité, etc. Par exemple, de nombreux matériaux durs ont tendance à être cassants, ce qui limite leurs cas d’utilisation.
Dans cet article, nous examinerons de plus près ce qu’est la dureté du matériau, comment elle est mesurée et comment comparer les différentes unités.
Qu’Est-Ce Que La Dureté Du Matériau?
La dureté est la mesure de la résistance d’un matériau à une déformation permanente localisée. La déformation permanente est également appelée déformation plastique. Alors que la déformation élastique signifie qu’un matériau ne change de forme que lors de l’application d’une force, une déformation plastique résultante signifie que le matériau ne retrouvera pas sa forme d’origine.
Certains matériaux sont naturellement durs. Par exemple, le tungstène est un métal incroyablement dur qui trouve une utilisation comme élément d’alliage dans les aciers à outils. Cela garantit que ce groupe d’aciers peut résister à l’usure même à des températures élevées pendant les opérations de coupe.
Le carbure cémenté, qui trouve beaucoup d’utilité dans les fraises, comprend également souvent du tungstène. Ces embouts d’outils de coupe remplaçables allongent considérablement la durée de vie des outils de coupe.
D’autre part, certains matériaux, y compris les métaux, sont mous au point de les rendre inutiles pour de nombreuses applications. L’or pur est si doux qu’il ne nécessite pas beaucoup d’efforts pour se gratter ou se plier. Par conséquent, l’ajout d’autres métaux comme l’argent, le cuivre et l’aluminium est essentiel pour améliorer sa dureté.
Avec certains matériaux, le traitement thermique est une possibilité d’induire une plus grande dureté de surface tout en maintenant les autres qualités du métal dans son noyau. Les arbres de machines subissent souvent ce processus pour garantir une durée de vie plus longue.
Un ingénieur doit également tenir compte du rapport de dureté lors de la création d’un concept de conception de produit. Par exemple, dans un ajustement de roulement et d’arbre, le roulement doit être plus souple car il est plus facile de le remplacer. Avec un mouvement constant, une pièce doit s’user et le choix appartient à l’ingénieur.
Types de dureté
Les matériaux se comportent différemment sous différents types de charges. Par exemple, un métal qui peut très bien encaisser un énorme impact ponctuel peut ne pas agir de la même manière lors d’un chargement continu.
Des essais de dureté doivent être effectués pour chaque cas afin qu’un choix éclairé puisse être fait pour l’application.
Les trois types de dureté sont la dureté aux rayures, au rebond et à l’indentation. La mesure de chaque type de dureté nécessite un ensemble d’outils différent. En outre, le même matériau aura des valeurs de dureté différentes pour chacun des types mentionnés ci-dessus.
Dureté d’indentation
Ce type de dureté se réfère à la résistance à la déformation permanente lors de la soumission d’un matériau à une charge continue.
La dureté d’indentation est ce à quoi les ingénieurs et les métallurgistes se réfèrent généralement lorsqu’ils parlent de dureté. La mesure de sa valeur est d’un intérêt primordial car le chargement continu est la forme de chargement la plus courante à laquelle les métaux sont soumis.
Dureté aux rayures
Ce type de dureté fait référence à la capacité d’un matériau à résister aux rayures sur la surface. Les rayures sont des indentations continues étroites dans la couche supérieure dues au contact avec un matériau tranchant et plus dur.
Le test de rayures est également couramment utilisé pour les matériaux fragiles tels que les céramiques car ils ne subissent pas de déformation plastique importante. Il est important de prendre en compte la dureté des rayures car certaines applications de matériaux sont très sensibles au marquage.
Prenons le cas d’une chemise de cylindre de moteur à titre d’exemple. Le grattage ou la notation peuvent avoir lieu pour diverses raisons. La surface du revêtement entre en contact avec une variété de métaux tels que les segments de piston, les particules étrangères dans le carburant ou l’huile de lubrification. Parfois, une mauvaise assise de la doublure peut y contribuer.
Les particules abrasives peuvent provoquer des rayures qui, à terme, dégradent les performances du moteur et coûtent plus cher en maintenance, en pièces de rechange et en consommation de carburant à long terme.
Au stade de la conception, le bon choix de métal tient compte de la dureté des matériaux avec lesquels il entrera en contact. La dureté de la doublure doit être supérieure aux matériaux avec lesquels elle interagira. Cela permet d’éviter de nombreux problèmes possibles.
Dureté de rebond ou dynamique
La dureté de rebond a plus à voir avec la dureté élastique que la dureté plastique. Le matériau absorbe l’énergie à l’impact et la renvoie au pénétrateur.
Un pénétrateur est un matériau de référence utilisé pour les essais de dureté. La dureté dynamique est généralement mesurée en faisant tomber un marteau à pointe de diamant sur l’éprouvette et en enregistrant le rebond du marteau après qu’il ait heurté la surface.
Plus la hauteur est proche de la hauteur de chute d’origine, plus la valeur de la dureté de rebond est élevée.
Obtenez votre devis de fabrication métallique en quelques secondes
-
Devis en quelques secondes
-
Délais courts
-
/div>Livraison par Fractoire
Obtenir un devis
Différentes unités de dureté
L’unité SI de dureté est N/ mm2. L’unité Pascal est donc également utilisée pour la dureté mais la dureté ne doit pas être confondue avec la pression.
Les différents types de dureté discutés ci-dessus ont des échelles de mesure différentes. Pour la dureté des rayures, de l’indentation et du rebond, les méthodes de mesure varient (par exemple Brinell, Rockwell, Knoop, Leeb et Meyer). Comme les unités sont dérivées de ces méthodes de mesure, elles ne conviennent pas à une comparaison directe.
Cependant, vous pouvez toujours utiliser une table de conversion pour comparer les valeurs Rockwell(B&C), Vickers et Brinell. Des tableaux comme ceux-ci ne sont pas précis à 100% mais donnent une bonne indication.
Brinell Hardness | Rockwell | Rockwell | Vickers | N/mm² |
HB | HRC | HRB | HV | |
469 | 50 | 117 | 505 | |
468 | 49 | 117 | 497 | |
456 | 48 | 116 | 490 | 1569 |
445 | 47 | 115 | 474 | 1520 |
430 | 46 | 115 | 458 | 1471 |
419 | 45 | 114 | 448 | 1447 |
415 | 44 | 114 | 438 | 1422 |
402 | 43 | 114 | 424 | 1390 |
388 | 42 | 113 | 406 | 1363 |
375 | 41 | 112 | 393 | 1314 |
373 | 40 | 111 | 388 | 1265 |
360 | 39 | 111 | 376 | 1236 |
348 | 38 | 110 | 361 | 1187 |
341 | 37 | 109 | 351 | 1157 |
331 | 36 | 109 | 342 | 1118 |
322 | 35 | 108 | 332 | 1089 |
314 | 34 | 108 | 320 | 1049 |
308 | 33 | 107 | 311 | 1035 |
300 | 32 | 107 | 303 | 1020 |
290 | 31 | 106 | 292 | 990 |
277 | 30 | 105 | 285 | 971 |
271 | 29 | 104 | 277 | 941 |
264 | 28 | 103 | 271 | 892 |
262 | 27 | 103 | 262 | 880 |
255 | 26 | 102 | 258 | 870 |
250 | 25 | 101 | 255 | 853 |
245 | 24 | 100 | 252 | 838 |
240 | 23 | 100 | 247 | 824 |
233 | 22 | 99 | 241 | 794 |
229 | 21 | 98 | 235 | 775 |
223 | 20 | 97 | 227 | 755 |
216 | 19 | 96 | 222 | 716 |
212 | 18 | 95 | 218 | 706 |
208 | 17 | 95 | 210 | 696 |
203 | 16 | 94 | 201 | 680 |
199 | 15 | 93 | 199 | 667 |
191 | 14 | 92 | 197 | 657 |
190 | 13 | 92 | 186 | 648 |
186 | 12 | 91 | 184 | 637 |
183 | 11 | 90 | 183 | 617 |
180 | 10 | 89 | 180 | 608 |
175 | 9 | 88 | 178 | 685 |
170 | 7 | 87 | 175 | 559 |
167 | 6 | 86 | 172 | 555 |
166 | 5 | 86 | 168 | 549 |
163 | 4 | 85 | 162 | 539 |
160 | 3 | 84 | 160 | 535 |
156 | 2 | 83 | 158 | 530 |
154 | 1 | 82 | 152 | 515 |
149 | 81 | 149 | 500 |
Dans toutes ces échelles, un matériau dur aura un nombre de dureté plus élevé.
Les unités couramment utilisées pour la mesure de la dureté sont:
- Numéro de dureté Brinell (HB)
- Numéro de dureté Vickers (HV)
- Numéro de dureté Rockwell (HRA, HRB, HRC, etc.)
- Valeur de dureté Leeb (HLD, HLS, HLE, etc.)
Dureté de mesure
Les différents types de dureté sont mesurés à l’aide de différents méthodes d’essai. Un point commun à toutes les méthodes est l’utilisation d’un pénétrateur pour créer l’indentation sur la surface de l’éprouvette. L’indentation fournit une représentation tangible de la dureté des matériaux et elle est facile à mesurer et à reproduire.
Les matériaux plus durs auront des indentations peu profondes et les matériaux plus mous auront des indentations plus profondes.
Essai de dureté Brinell

Essai de dureté Brinell
L’essai Brinell a été l’un des premiers essais de dureté largement acceptés pour la mesure de la dureté par indentation. Dans le test Brinell, une bille d’acier de 10 mm de diamètre est utilisée comme pénétrateur pour créer une empreinte sur l’éprouvette afin de calculer son nombre de dureté Brinell.
La balle est maintenue en place pendant un temps prédéterminé, généralement 30 secondes, et une force est appliquée sur la balle. Cette force varie en fonction du métal d’essai mesuré.
La charge standard est de 3000 kg, mais elle peut être réduite à 500 kg pour les métaux plus mous. Pour les métaux plus durs, une bille en carbure de tungstène peut être utilisée pour empêcher la distorsion de la bille. L’unité de dureté HB (ou HBN) sera changée en HBW en cas de tungstène pour notifier son utilisation (Tungstène = Wolfram en allemand / suédois).
Lors du retrait du pénétrateur, la dent est observée avec un microscope de faible puissance et la taille est calculée en prenant la moyenne des mesures à angle droit.
À la fin de l’essai Brinell, le nombre de dureté est calculé comme suit:
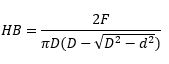
, où
Force F, N
Diamètre du pénétrateur D, mm
Diamètre du renfoncement d, mm
Dureté Rockwell Test

Test de dureté Rockwell
L’essai de dureté Rockwell est la méthode la plus couramment utilisée pour les mesures de dureté par indentation. La valeur de la dureté Rockwell est accompagnée de l’échelle utilisée.
En fonction du matériau testé, une échelle appropriée doit être sélectionnée. Cette échelle de dureté donne des informations sur le type de combinaison pénétrateur-charge utilisée.
Il y a un total de 30 échelles disponibles au choix. C’est ce qui fait de Rockwell un test étalon pour mesurer la dureté d’un large éventail de matériaux. Même les mesures de dureté des matériaux céramiques et composites sont possibles. Les échelles les plus couramment utilisées sont « B” et ”C ».
Dans l’essai de dureté Rockwell, avant d’appliquer la charge d’essai, une petite charge mineure est appliquée pour placer le pénétrateur dans l’éprouvette et éliminer l’effet de toute irrégularité de surface. Cela fournit une meilleure précision.
Ensuite, de manière similaire à l’essai Brinell, le pénétrateur est utilisé pour créer une impression sur le matériau en appliquant la charge d’essai également appelée charge majeure. L’empreinte est ensuite mesurée pour déterminer la dureté. Une jauge à cadran est utilisée pour enregistrer la déformation.
L’augmentation nette de la dimension de la dent (entre l’application d’une charge mineure et d’une charge majeure) est prise en compte pour le calcul de la valeur de dureté.
Il est nécessaire de spécifier la vitesse de chargement. Dans les métaux mous, des vitesses variables d’application de la charge peuvent produire une différence appréciable dans la valeur finale. Il est important de surveiller attentivement que le taux de chargement est conforme à la norme.
La formule de dureté Rockwell est:
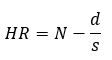
, où
Facteur d’échelle N en fonction de l’échelle utilisée
facteur d’échelle s en fonction de l’échelle utilisée
d – profondeur d’indentation permanente par rapport à une charge mineure, mm
Essai de dureté Vickers
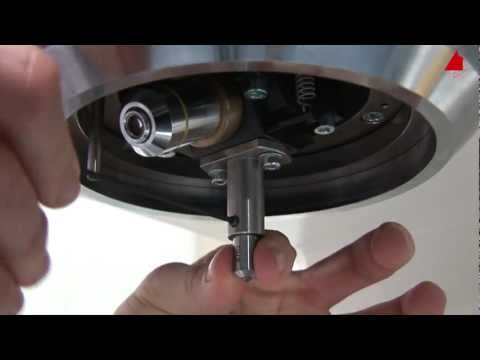
Essai de dureté Vickers
La troisième façon de mesurer la dureté du matériau consiste à utiliser le test Vickers. Ceci est particulièrement adapté aux matériaux plus mous qui n’ont pas besoin de charges élevées. Avec des matériaux souples, la méthode Vickers offre une meilleure précision.
De plus, le calcul de la valeur de dureté est plus facile, car Vickers utilise le même pénétrateur de diamant pour tous les matériaux. Ainsi, peaufiner la formule n’est pas nécessaire.
Une autre caractéristique importante est l’utilisation d’une loupe, permettant de tester des zones avec une microstructure spécifique.
Tout d’abord, le testeur doit placer la pièce sur la machine et utiliser le microscope pour trouver la hauteur appropriée. Ensuite, en utilisant les images, le bon endroit est déterminé.
Le pénétrateur en diamant a la forme d’une pyramide à quatre faces. Après avoir touché la pièce, la machine atteint rapidement la valeur de force prédéterminée. Il reste à la même charge pendant un certain temps.
Ensuite, la mesure de l’indentation a lieu. Le calcul de la valeur de dureté Vickers utilise la formule suivante:
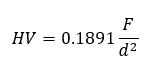
, où
Force F, N
diagonale d’indentation d, mm
Test de dureté Mohs
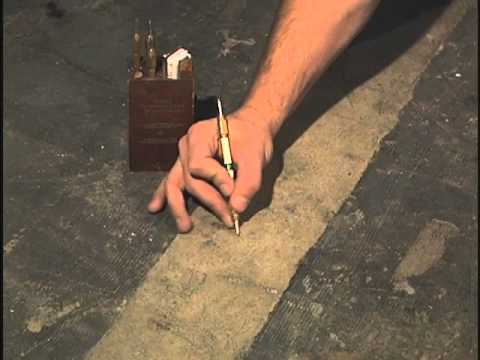
Test de dureté MOHS
Le minéralogiste allemand Mohs a d’abord conçu le test de dureté Mohs pour mesurer la dureté des rayures des matériaux. Dans cet essai, le matériau est rayé avec un matériau de référence qui a une dureté définie.
Une valeur numérique de dureté est attribuée au matériau d’essai sur la base des résultats de l’essai. L’essai de dureté Mohs utilise 10 matériaux de référence de dureté variable comme échelle pour l’essai.
Le matériau le plus doux utilisé est le talc (valeur = 1) et le matériau le plus dur est le diamant (valeur = 10). Étant donné que les références utilisées pour l’échelle de Mohs n’ont pas d’augmentation graduée, l’échelle de Mohs manque de précision et n’est qu’une mesure approximative de la dureté.
Aujourd’hui, les essais de rayure modernes sont effectués à l’aide de pénétrateurs à diamant Rockwell en grattant l’éprouvette sur une longueur spécifique pressée par une valeur de charge sélectionnée.
Essai de scléroscope
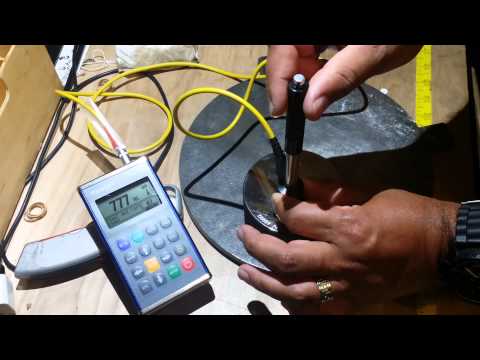
Essai de dureté de rebond
Un scléroscope est un dispositif utilisé pour mesurer le rebond ou la dureté dynamique des matériaux. La configuration se compose d’un tube de verre vertical creux relié à un support. À travers ce tube, un marteau en diamant est déposé sur l’éprouvette et le rebond du marteau est enregistré.
Le marteau en diamant tombe d’une hauteur fixe sous son propre poids. Au contact de l’éprouvette, le marteau rebondit. Ce rebond sera plus élevé pour les matériaux avec une dureté plus élevée.
Le rebond sera plus faible pour un métal mou car une partie de l’énergie d’impact sera épuisée en créant une bosse sur la surface d’essai. Le tube de verre a des gradients pour mesurer la hauteur du rebond. La dureté du rebond est mesurée en unités shore.