A keménység olyan anyagminőség, amely ellenáll a lokalizált deformációnak. Különösen fontos lehet, ha megfelelő anyagot keres olyan környezethez, amely kis részecskéket tartalmaz, amelyek anyagkopást okozhatnak. A puha anyagok behúzódnak, míg a kemények ellenállnak az alakváltozásnak.
a keménységet más anyagtulajdonságokkal, például szilárdsággal, rugalmassággal stb.összefüggésben kell megtekinteni. Például sok kemény anyag általában törékeny, korlátozva azok használatát-esetek.
ebben a cikkben közelebbről megvizsgáljuk, hogy milyen anyagkeménység van, hogyan mérik, és hogyan lehet összehasonlítani a különböző egységeket.
mi az anyagkeménység?
a keménység az anyag lokalizált állandó deformációval szembeni ellenállásának mértéke. Az állandó deformációt műanyag deformációnak is nevezik. Míg az elasztikus deformáció azt jelenti, hogy az anyag csak az erő alkalmazása során változtatja meg alakját, az ebből eredő műanyag deformáció azt jelenti, hogy az anyag nem tér vissza eredeti alakjához.
egyes anyagok természetesen kemények. Például a volfrám hihetetlenül kemény fém, amely ötvözőelemként használja a szerszámacélokat. Ez biztosítja, hogy ez az acélcsoport ellenálljon a kopásnak még magas hőmérsékleten is a vágási műveletek során.
a cementált karbid, amely nagy haszonnal jár az őrlőgépekben, gyakran tartalmaz volfrámot is. Ezek a cserélhető vágószerszámok jelentősen meghosszabbítják a vágószerszámok élettartamát.
másrészt egyes anyagok, beleértve a fémeket is, lágyak arra a pontra, hogy sok alkalmazáshoz használhatatlanná teszik őket. A tiszta arany olyan puha, hogy karcolás vagy hajlítás nem igényel sok erőfeszítést. Ezért más fémek, például ezüst, réz és alumínium hozzáadása elengedhetetlen a keménység javításához.
egyes anyagokkal a hőkezelés nagyobb felületi keménységet válthat ki, miközben megőrzi a fém többi tulajdonságát a magjában. A géptengelyek gyakran ezt a folyamatot végzik, hogy garantálják a hosszabb élettartamot.
a mérnöknek figyelembe kell vennie a keménység arányát a terméktervezési koncepció létrehozásakor. Például csapágyazásnál és tengelyelrendezésnél a csapágynak lágyabbnak kell lennie, mert könnyebben cserélhető. Állandó mozgással az egyik részt viselni kell, a választás pedig a mérnöktől függ.
A keménység típusai
az anyagok eltérő módon viselkednek a különböző típusú terheléseknél. Például egy olyan fém, amely rendkívül jól képes egy hatalmas egyszeri ütésre, nem működhet ugyanúgy a folyamatos terhelés során.
keménységi vizsgálatot kell végezni minden esetben, hogy jól tájékozott döntést lehessen hozni az alkalmazáshoz.
a keménység három típusa a karcolás, a visszapattanás és a bemélyedés keménysége. Az egyes keménységi típusok mérése különböző szerszámkészletet igényel. Ugyanez az anyag különböző keménységi értékekkel rendelkezik a fent említett típusok mindegyikéhez.
behúzási keménység
Ez a keménységi típus az állandó deformációval szembeni ellenállásra utal, amikor egy anyagot folyamatos terhelésnek vetnek alá.
a bemélyedés keménysége az, amire a mérnökök és a metallurgisták általában hivatkoznak, amikor a keménységről beszélnek. Értékének mérése elsődleges fontosságú, mivel a folyamatos terhelés a fémek rakodásának leggyakoribb formája.
Scratch keménység
Ez a fajta keménység az anyag azon képességére utal, hogy ellenálljon a karcolásoknak a felületen. A karcolások keskeny, folyamatos bemélyedések a felső rétegben, éles, keményebb anyaggal való érintkezés miatt.
karcolás vizsgálat is általánosan használt törékeny anyagok, mint például a kerámia, mivel nem mennek keresztül jelentős műanyag deformáció. Fontos figyelembe venni a karcolás keménységét, mivel egyes anyagalkalmazások nagyon érzékenyek a pontozásra.
példaként vegye figyelembe a motorhengeres bélés esetét. A karcolás vagy a pontozás különböző okok miatt történhet. A bélés felülete számos fémmel érintkezik, például dugattyúgyűrűkkel, idegen részecskékkel az üzemanyagban vagy a kenőolajban. Néha a bélés nem megfelelő ülése hozzájárulhat ehhez.
a csiszolószemcsék olyan karcolásokat okozhatnak, amelyek végső soron rontják a motor teljesítményét, és hosszabb távon többe kerülnek a karbantartás, a pótalkatrészek és az üzemanyag-fogyasztás terén.
a tervezési szakaszban a megfelelő fémválasztás figyelembe veszi az anyagok keménységét, amellyel kapcsolatba kerül. A bélés keménységének nagyobbnak kell lennie, mint az anyagok, amelyekkel kölcsönhatásba lép. Ez segít elkerülni számos lehetséges kérdést.
Rebound vagy dinamikus keménység
a Rebound keménységnek több köze van a rugalmas keménységhez, mint a műanyag keménységhez. Az anyag elnyeli az energiát a becsapódáskor, majd visszaadja az indenterbe.
az indenter a keménységvizsgálathoz használt referenciaanyag. A dinamikus keménységet általában úgy mérik, hogy egy gyémánt hegyű kalapácsot dobnak a tesztdarabra, majd rögzítik a kalapács ugrását, miután a felület megütötte.
minél közelebb van a magasság az eredeti csepegtető magassághoz, annál nagyobb a rebound keménység értéke.
a fémmegmunkáló idézet másodperc
-
Idézet másodperc
-
Rövid átfutási idők
-
Szállítás Fractory
Get idézet
a Különböző Keménységű Egységek
Az SI egység a keménység, N/mm2. A Pascal egységet tehát keménységre is használják, de a keménységet nem szabad összekeverni a nyomással.
a fent tárgyalt különböző keménységi típusok különböző mérési skálákkal rendelkeznek. A karcolás, a bemélyedés és a rebound keménység esetében a mérési módszerek eltérőek (pl. Brinell, Rockwell, Knoop, Leeb és Meyer). Mivel az egységek ezekből a mérési módszerekből származnak, nem alkalmasak közvetlen összehasonlításra.
a Rockwell (B & C), Vickers és Brinell értékek összehasonlításához azonban mindig használhat konverziós táblázatot. Az ilyen táblázatok nem 100% – ban pontosak, de jó jelzést adnak.
Brinell Hardness | Rockwell | Rockwell | Vickers | N/mm² |
HB | HRC | HRB | HV | |
469 | 50 | 117 | 505 | |
468 | 49 | 117 | 497 | |
456 | 48 | 116 | 490 | 1569 |
445 | 47 | 115 | 474 | 1520 |
430 | 46 | 115 | 458 | 1471 |
419 | 45 | 114 | 448 | 1447 |
415 | 44 | 114 | 438 | 1422 |
402 | 43 | 114 | 424 | 1390 |
388 | 42 | 113 | 406 | 1363 |
375 | 41 | 112 | 393 | 1314 |
373 | 40 | 111 | 388 | 1265 |
360 | 39 | 111 | 376 | 1236 |
348 | 38 | 110 | 361 | 1187 |
341 | 37 | 109 | 351 | 1157 |
331 | 36 | 109 | 342 | 1118 |
322 | 35 | 108 | 332 | 1089 |
314 | 34 | 108 | 320 | 1049 |
308 | 33 | 107 | 311 | 1035 |
300 | 32 | 107 | 303 | 1020 |
290 | 31 | 106 | 292 | 990 |
277 | 30 | 105 | 285 | 971 |
271 | 29 | 104 | 277 | 941 |
264 | 28 | 103 | 271 | 892 |
262 | 27 | 103 | 262 | 880 |
255 | 26 | 102 | 258 | 870 |
250 | 25 | 101 | 255 | 853 |
245 | 24 | 100 | 252 | 838 |
240 | 23 | 100 | 247 | 824 |
233 | 22 | 99 | 241 | 794 |
229 | 21 | 98 | 235 | 775 |
223 | 20 | 97 | 227 | 755 |
216 | 19 | 96 | 222 | 716 |
212 | 18 | 95 | 218 | 706 |
208 | 17 | 95 | 210 | 696 |
203 | 16 | 94 | 201 | 680 |
199 | 15 | 93 | 199 | 667 |
191 | 14 | 92 | 197 | 657 |
190 | 13 | 92 | 186 | 648 |
186 | 12 | 91 | 184 | 637 |
183 | 11 | 90 | 183 | 617 |
180 | 10 | 89 | 180 | 608 |
175 | 9 | 88 | 178 | 685 |
170 | 7 | 87 | 175 | 559 |
167 | 6 | 86 | 172 | 555 |
166 | 5 | 86 | 168 | 549 |
163 | 4 | 85 | 162 | 539 |
160 | 3 | 84 | 160 | 535 |
156 | 2 | 83 | 158 | 530 |
154 | 1 | 82 | 152 | 515 |
149 | 81 | 149 | 500 |
mindegyik mérlegben a kemény anyagnak nagyobb keménységi száma lesz.
a keménységméréshez általánosan használt egységek a következők:
- Brinell keménységi szám (HB)
- Vickers keménységi szám (HV)
- Rockwell keménységi szám (HRA, HRB, HRC stb.)
- Leeb keménységi érték (HLD, HLS, HLE stb.)
keménység mérése
a különböző keménységi típusokat a különböző vizsgálati módszerek. Az összes módszer közössége az indenter használata a bemélyedés létrehozásához a tesztdarab felületén. A bemélyedés kézzelfogható képet ad az anyagok keménységéről, könnyen mérhető és megismételhető.
A keményebb anyagok sekély bemélyedésekkel, a lágyabb anyagok mélyebb bemélyedésekkel rendelkeznek.
Brinell keménységi teszt

Brinell keménységi teszt
a Brinell-teszt egyike volt az első széles körben elfogadott keménységi tesztnek a bemélyedési keménység mérésére. A Brinell-tesztben egy 10 mm átmérőjű acélgolyót használnak indenterként, hogy benyomást keltsenek a vizsgálati darabra a Brinell keménységi számának kiszámításához.
a labdát egy előre meghatározott ideig, általában 30 másodpercig tartják a helyén, majd egy erőt alkalmaznak a labdára. Ez az erő a vizsgált fémtől függően változik.
a standard terhelés 3000 kg, de lágyabb fémeknél 500 kg-ra csökkenthető. A keményebb fémek esetében egy volfrámkarbid gömb használható a labda torzulásának megakadályozására. A HB (vagy HBN) keménységegységet volfrám esetén HBW-re cserélik, hogy értesítsék annak használatát (Tungsten=Wolfram német/svéd nyelven).
az indenter eltávolításakor a dent egy kis teljesítményű mikroszkóppal figyelhető meg, a méretet a mérések átlagának derékszögben történő figyelembevételével számítják ki.
a Brinell-vizsgálat befejezése után a keménységi szám a következőképpen kerül kiszámításra:
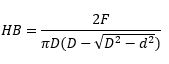
, ahol a
F – erő, N
D – indenter átmérő, mm
d – behúzás átmérő, mm
Rockwell Keménység Teszt

Rockwell Keménység Teszt
Rockwell keménység teszt a leggyakrabban használt módszer a behúzás keménység mérés. A Rockwell keménység értékét az alkalmazott skála kíséri.
a vizsgált anyagtól függően megfelelő skálát kell kiválasztani. Ez a keménységi skála információt nyújt az alkalmazott indenter-load kombináció típusáról.
összesen 30 mérleg közül lehet választani. Ez teszi a Rockwell-t mérőszalag-tesztnek az anyagok széles skálájának keménységének mérésére. Kerámia és kompozit anyagkeménységmérés is lehetséges. A leggyakrabban használt mérlegek “B” és “C”.
a Rockwell keménységi vizsgálat során, a vizsgálati terhelés alkalmazása előtt, egy kis kisebb terhelést alkalmaznak az indenter behelyezésére a vizsgálati darabba, és eltávolítják a felületi szabálytalanságok hatását. Ez jobb pontosságot biztosít.
ezután hasonló a Brinell teszthez, az indentert arra használják, hogy benyomást keltsen az anyagra a nagy terhelésnek is nevezett vizsgálati terhelés alkalmazásával. Ezután megmérjük a benyomást a keménység meghatározására. A deformáció rögzítéséhez tárcsás mérőeszközt használnak.
a keménységérték kiszámításához figyelembe kell venni a Dent dimenzió nettó növekedését (kisebb és nagyobb terhelés alkalmazása között).
a betöltési sebesség megadása szükséges. A lágy fémekben a terhelés változó sebessége észrevehető különbséget eredményezhet a végső értékben. Fontos gondosan ellenőrizni, hogy a terhelés mértéke a szabványnak megfelelően van-e.
a Rockwell keménység képlete:
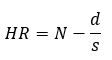
, ahol a
N – skála faktor attól függően, hogy a skála
s – skála faktor attól függően, hogy a skála
d – mélysége állandó behúzás képest kisebb terhelés, mm
Vickers Keménység Teszt
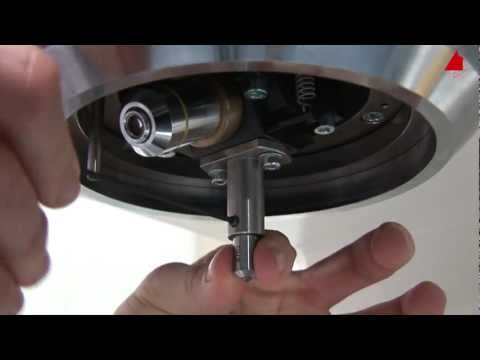
Vickers Keménység Teszt
A harmadik módja, a mérési anyag keménysége segítségével a Vickers teszt. Ez különösen alkalmas olyan lágyabb anyagokra, amelyek nem igényelnek nagy terhelést. Puha anyagokkal a Vickers módszer jobb pontosságot biztosít.
a keménységi érték kiszámítása is könnyebb, mivel a Vickers ugyanazt a gyémánt indentert használja minden anyaghoz. Így a képlet módosítása nem szükséges.
egy másik fontos jellemző a nagyító használata, amely lehetővé teszi egy adott mikroszerkezettel rendelkező területek tesztelését.
először is, a tesztelőnek az alkatrészt a gépre kell helyeznie, majd a mikroszkóp segítségével meg kell találnia a megfelelő magasságot. Ezután a képek segítségével meghatározzuk a megfelelő helyet.
a gyémánt indenter négyoldalas piramis alakú. Az alkatrész megérintése után a gép hamarosan eléri az előre meghatározott erőértéket. Egy bizonyos ideig ugyanabban a terhelésben marad.
ezután a bemélyedés mérése megtörténik. A Vickers keménységi érték kiszámítása a következő képletet használja:
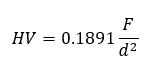
, ahol a
F – erő, N
d – behúzás átlós, mm
Mohs-féle Keménységi Teszt
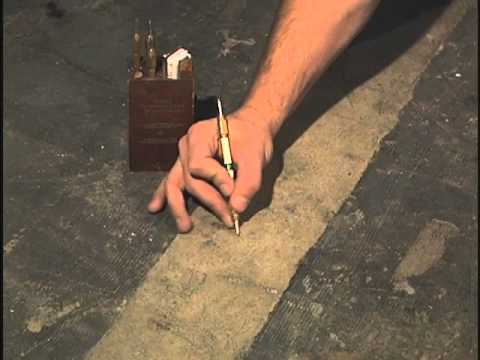
MOHS-féle Keménységi Teszt
a német mineralógus Mohs első kidolgozott a Mohs-féle keménységi teszt, hogy az intézkedés a semmiből keménységű anyagok. Ebben a vizsgálatban az anyagot egy meghatározott keménységű referenciaanyaggal karcolják meg.
a vizsgálati anyaghoz a vizsgálat eredményei alapján numerikus keménységi értéket rendelünk. Mohs keménység teszt használ 10 referenciaanyagok különböző keménységű, mint a skála a vizsgálat.
a legpuhább anyag a talkum (érték=1), a legnehezebb anyag pedig a gyémánt (érték=10). Tekintettel arra, hogy a Mohs-skálán használt referenciáknak nincs fokozatos növekedése, a Mohs-skálán nincs pontosság, és csak durva keménységmérés.
a Mai, modern karcolás vizsgálatokat elvégezni Rockwell gyémánt indenters vakarja a vizsgálati darab egy meghatározott ideig nyomva által kiválasztott terhelési érték.
Scleroscope Test
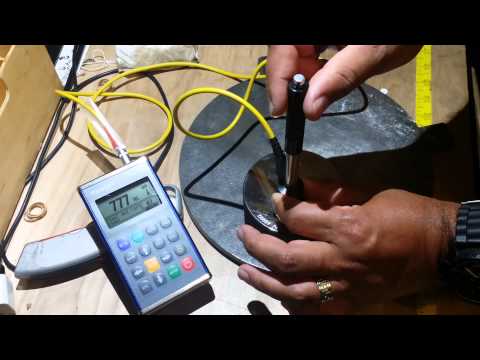
Rebound keménységi teszt
a scleroscope olyan eszköz, amelyet az anyagok visszapattanó vagy dinamikus keménységének mérésére használnak. A beállítás áll egy üreges függőleges üvegcső csatlakozik egy állvány. Ezen a csövön keresztül egy gyémánt kalapácsot dobnak a próbadarabra, majd rögzítik a kalapács visszafordulását.
a gyémánt kalapács saját súlya alatt rögzített magasságból esik le. Amikor érintkezésbe kerül a teszt darabbal, a kalapács visszapattan. Ez a visszafordulás magasabb lesz a nagyobb keménységű anyagok esetében.
a visszafordulás alacsonyabb lesz egy puha fém esetében, mivel az ütközési energia egy része kimerül a vizsgálati felület horpadásának létrehozásakor. Az üvegcső színátmenetekkel rendelkezik a visszafordulás magasságának mérésére. A Rebound keménységét parti egységekben mérik.