kovuus on materiaalin laatu, joka kestää paikallista muodonmuutosta. Se voi olla erityisen tärkeää etsittäessä sopivaa materiaalia ympäristöön, jossa on vähän hiukkasia, jotka voivat aiheuttaa materiaalin kulumista. Pehmeät materiaalit kärsivät painaumista, kun taas kovat kestävät minkä tahansa muotomuutoksen.
kovuutta on tarkasteltava yhteydessä muihin materiaalin ominaisuuksiin, kuten lujuuteen, kimmoisuuteen jne. Esimerkiksi monet kovat materiaalit ovat helposti hauraita, mikä rajoittaa niiden käyttötapauksia.
tässä artikkelissa tarkastellaan tarkemmin, mitä materiaalin kovuus on, miten se mitataan ja miten eri yksiköitä verrataan keskenään.
mikä on materiaalin kovuus?
kovuus on materiaalin paikallisen pysyvän muodonmuutoskestävyyden mitta. Pysyvää muodonmuutosta kutsutaan myös plastiseksi muodonmuutokseksi. Vaikka elastinen muodonmuutos tarkoittaa sitä, että materiaali muuttaa muotoaan vain voiman käytön aikana, tuloksena oleva plastinen muodonmuutos tarkoittaa, että materiaali ei palaa alkuperäiseen muotoonsa.
jotkut materiaalit ovat luonnostaan kovia. Esimerkiksi volframi on uskomattoman kova metalli, joka löytää käyttöä seosaineena työkaluteräksissä. Tämä varmistaa, että tämä teräsryhmä kestää kulumista korkeissakin lämpötiloissa leikkausten aikana.
kovametalli, jota käytetään paljon jyrsimissä, sisältää usein myös volframia. Nämä vaihdettavat leikkuutyökalun bitit pidentävät leikkuutyökalujen käyttöikää huomattavasti.
toisaalta jotkin materiaalit, kuten metallit, ovat niin pehmeitä, että ne ovat hyödyttömiä moniin sovelluksiin. Puhdas kulta on niin pehmeää, että sen raapiminen tai taivuttaminen ei vaadi paljon vaivannäköä. Siksi muiden metallien, kuten hopean, kuparin ja alumiinin, lisääminen on välttämätöntä sen kovuuden parantamiseksi.
joillakin materiaaleilla lämpökäsittelyllä on mahdollista saada aikaan suurempi pintakovuus säilyttäen samalla metallin muut ominaisuudet sen ytimessä. Koneen akselit käyvät usein läpi tämän prosessin pidemmän käyttöiän takaamiseksi.
insinöörin on otettava huomioon myös kovuuden suhde tuotesuunnittelukonseptia luodessaan. Esimerkiksi laakerin ja akselin istuvuudessa laakerin on oltava pehmeämpi, koska ne on helpompi vaihtaa. Jatkuvassa liikkeessä yksi osa joutuu kulumaan ja valinta on insinöörin tehtävä.
Kovuustyypit
materiaalit käyttäytyvät eri tavoin erityyppisissä kuormituksissa. Esimerkiksi metalli, joka voi kestää valtavan kerran iskun erittäin hyvin, ei välttämättä toimi samalla tavalla jatkuvan kuormituksen aikana.
kovuuskoe on tehtävä jokaiselle tapaukselle, jotta käyttökohteesta voidaan tehdä hyvin perusteltu valinta.
kolme kovuustyyppiä ovat scratch -, rebound-ja sisennyskovuus. Kunkin kovuustyypin mittaaminen vaatii erilaisia työkaluja. Samalla materiaalilla on myös eri kovuusarvot kullekin edellä mainitulle tyypille.
Sisennyskovuus
tällä kovuustyypillä tarkoitetaan pysyvän muodonmuutoksen kestoa altistettaessa materiaalia jatkuvalle kuormitukselle.
Sisennyskovuus on se, mihin insinöörit ja metallurgit yleensä viittaavat kovuudesta puhuessaan. Sen arvon mittaaminen on ensisijaisen tärkeää, koska jatkuva kuormitus on yleisin metallien kuormittamisen muoto.
Naarmuuntumiskovuus
tällä kovuustyypillä tarkoitetaan materiaalin kykyä vastustaa pinnan naarmuja. Naarmut ovat kapeita jatkuvia painumia ylemmässä kerroksessa johtuen kosketuksesta terävään, kovempaan materiaaliin.
Naarmuuntumistestausta käytetään yleisesti myös hauraille materiaaleille, kuten keramiikalle, koska ne eivät käy läpi merkittävää plastista muodonmuutosta. On tärkeää harkita tyhjästä kovuus, koska jotkut materiaali sovellukset ovat erittäin herkkiä pisteytys.
esimerkkinä voidaan pitää moottorin sylinterivuorausta. Raapiminen tai pisteytys voi tapahtua eri syistä. Vuorauksen pinta joutuu kosketuksiin erilaisten metallien, kuten männänrenkaiden, vieraiden hiukkasten kanssa polttoaineessa tai voiteluöljyssä. Joskus väärin istuma liner voi edistää sitä.
hankaavat hiukkaset voivat aiheuttaa naarmuja, jotka lopulta heikentävät moottorin suorituskykyä ja maksavat pidemmällä aikavälillä enemmän huollossa, varaosissa ja polttoaineenkulutuksessa.
suunnitteluvaiheessa oikea metallivalinta ottaa huomioon niiden materiaalien kovuuden, joiden kanssa se joutuu kosketuksiin. Vuorauksen kovuuden on oltava suurempi kuin materiaalit, joiden kanssa se on vuorovaikutuksessa. Tämä auttaa välttämään monia mahdollisia kysymyksiä.
Rebound tai dynaaminen kovuus
Rebound-kovuus liittyy enemmän elastiseen kovuuteen kuin muoviseen kovuuteen. Materiaali absorboi törmäyksessä energiaa ja palauttaa sen sisennimeen.
sisennys on kovuuskokeissa käytettävä vertailumateriaali. Dynaaminen kovuus mitataan yleensä pudottamalla timanttikärkinen vasara testikappaleeseen ja tallentamalla vasaran pomppu sen osuttua pintaan.
mitä lähempänä korkeus on alkuperäistä pudotuskorkeutta, sitä suurempi on rebound-kovuuden arvo.
Hanki metalliteollisuuden lainaus sekunneissa
-
lainaus sekunneissa
-
fractorin toimittama
Lyhyet läpimenoajat
get sitaatti
eri kovuusyksiköt
kovuuden SI-yksikkö on N / mm2. Yksikkö Pascalia käytetään siis myös kovuuteen, mutta kovuutta ei saa sekoittaa paineeseen.
edellä mainituilla kovuustyypeillä on erilaiset mitta-asteikot. Scratch -, sisennys-ja rebound-kovuudessa mittausmenetelmät vaihtelevat (esim.Brinell, Rockwell, Knoop, Leeb ja Meyer). Koska yksiköt johdetaan näistä mittausmenetelmistä, ne eivät sovellu suoraan vertailuun.
voidaan kuitenkin aina käyttää muunnostaulukkoa Rockwellin (b & C), Vickersin ja Brinellin arvojen vertailuun. Tällaiset taulukot eivät ole 100% tarkkoja, mutta antavat hyvän osviittaa.
Brinell Hardness | Rockwell | Rockwell | Vickers | N/mm² |
HB | HRC | HRB | HV | |
469 | 50 | 117 | 505 | |
468 | 49 | 117 | 497 | |
456 | 48 | 116 | 490 | 1569 |
445 | 47 | 115 | 474 | 1520 |
430 | 46 | 115 | 458 | 1471 |
419 | 45 | 114 | 448 | 1447 |
415 | 44 | 114 | 438 | 1422 |
402 | 43 | 114 | 424 | 1390 |
388 | 42 | 113 | 406 | 1363 |
375 | 41 | 112 | 393 | 1314 |
373 | 40 | 111 | 388 | 1265 |
360 | 39 | 111 | 376 | 1236 |
348 | 38 | 110 | 361 | 1187 |
341 | 37 | 109 | 351 | 1157 |
331 | 36 | 109 | 342 | 1118 |
322 | 35 | 108 | 332 | 1089 |
314 | 34 | 108 | 320 | 1049 |
308 | 33 | 107 | 311 | 1035 |
300 | 32 | 107 | 303 | 1020 |
290 | 31 | 106 | 292 | 990 |
277 | 30 | 105 | 285 | 971 |
271 | 29 | 104 | 277 | 941 |
264 | 28 | 103 | 271 | 892 |
262 | 27 | 103 | 262 | 880 |
255 | 26 | 102 | 258 | 870 |
250 | 25 | 101 | 255 | 853 |
245 | 24 | 100 | 252 | 838 |
240 | 23 | 100 | 247 | 824 |
233 | 22 | 99 | 241 | 794 |
229 | 21 | 98 | 235 | 775 |
223 | 20 | 97 | 227 | 755 |
216 | 19 | 96 | 222 | 716 |
212 | 18 | 95 | 218 | 706 |
208 | 17 | 95 | 210 | 696 |
203 | 16 | 94 | 201 | 680 |
199 | 15 | 93 | 199 | 667 |
191 | 14 | 92 | 197 | 657 |
190 | 13 | 92 | 186 | 648 |
186 | 12 | 91 | 184 | 637 |
183 | 11 | 90 | 183 | 617 |
180 | 10 | 89 | 180 | 608 |
175 | 9 | 88 | 178 | 685 |
170 | 7 | 87 | 175 | 559 |
167 | 6 | 86 | 172 | 555 |
166 | 5 | 86 | 168 | 549 |
163 | 4 | 85 | 162 | 539 |
160 | 3 | 84 | 160 | 535 |
156 | 2 | 83 | 158 | 530 |
154 | 1 | 82 | 152 | 515 |
149 | 81 | 149 | 500 |
kaikissa näissä asteikoissa kovalla materiaalilla on suurempi kovuusluku.
yleisesti käytettyjä kovuuden mittayksiköitä ovat:
- Brinellin Kovuusluku (HB)
- Vickersin kovuusluku (HV)
- Rockwellin kovuusluku (HRA, HRB, HRC jne)
- Leebin kovuusarvo (HLD, HLS, Hle jne)
kovuuden mittaaminen
eri kovuustyypit mitataan käyttäen erilaisia testausmenetelmiä. Kaikille menetelmille on yhteistä sisennyksen käyttö koekappaleen pinta-alan sisennyksen aikaansaamiseksi. Sisennys antaa konkreettisen esityksen materiaalien kovuudesta ja se on helppo mitata ja monistaa.
kovemmilla materiaaleilla on matalat painaumat ja pehmeämmillä materiaaleilla syvemmät painaumat.
Brinellin kovuuskoe

Brinellin kovuuskoe
Brinellin testi oli ensimmäisiä yleisesti hyväksyttyjä kovuuskokeita sisennyksen kovuuden mittauksessa. Brinellin testissä käytetään halkaisijaltaan 10 mm: n teräskuulaa, joka muodostaa jäljen testikappaleeseen sen Brinell-kovuusluvun laskemiseksi.
palloa pidetään paikoillaan ennalta määrätyn ajan, yleensä 30 sekuntia, ja palloon kohdistetaan voima. Tämä voima vaihtelee mitattavan testimetallin mukaan.
standardikuorma on 3 000 kg, mutta pehmeämpien metallien kohdalla se voidaan pienentää 500 kg: aan. Kovemmille metalleille voidaan käyttää volframikarbidikuulaa pallon vääristymisen estämiseksi. Kovuusyksikkö HB (tai HBN) muutetaan volframin osalta HBW: ksi sen käytön ilmoittamiseksi (volframi=volframi saksaksi/ruotsiksi).
kun sisennys poistetaan, lommo havaitaan pienitehoisella mikroskoopilla ja koko lasketaan ottamalla mittausten keskiarvo suorassa kulmassa.
Brinellin testin päätyttyä kovuusluku lasketaan seuraavasti:
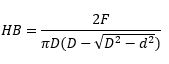
, missä
F – voima, n
D – sisennyksen halkaisija, mm
d – sisennyksen halkaisija, mm
Rockwell kovuuskoe

Rockwellin kovuuskoe
Rockwellin kovuuskoe on yleisimmin käytetty menetelmä sisennyskovuuden mittauksissa. Rockwellin kovuuden arvoon liittyy käytetty asteikko.
testattavasta materiaalista riippuen on valittava sopiva mittakaava. Tämä kovuusasteikko antaa tiedon käytetyn indenter-load-yhdistelmän tyypistä.
tarjolla on yhteensä 30 asteikkoa, joista valita. Tämä tekee Rockwellista mittapuukokeen, jolla mitataan monenlaisten materiaalien kovuutta. Jopa keraamisten ja komposiittimateriaalien kovuusmittaukset ovat mahdollisia. Yleisimmin käytetyt asteikot ovat ”B” ja ”C”.
Rockwellin kovuustestissä käytetään ennen testikuormituksen levittämistä pientä pientä kuormaa, joka asetetaan testikappaleen sisennimen paikalleen ja poistetaan mahdolliset pinnan epätasaisuudet. Näin saadaan parempi tarkkuus.
tällöin käytetään brinellin testin tapaan sisennintä, jonka avulla materiaaliin luodaan vaikutelma käyttämällä testikuormaa, jota kutsutaan myös suurkuormaksi. Sen jälkeen mitataan vaikutelma kovuuden määrittämiseksi. Dial mittari käytetään tallentaa muodonmuutoksen.
kovuusarvoa laskettaessa otetaan huomioon lommomitan nettolisäys (pienen ja suuren kuormituksen välillä).
lastausnopeuden määrittäminen on tarpeen. Pehmeissä metalleissa kuormituksen vaihteleva nopeus voi tuottaa merkittävän eron lopulliseen arvoon. On tärkeää seurata tarkasti, että lastausnopeus on standardin mukainen.
Rockwellin kovuuden kaava on:
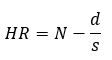
, jossa
n – asteikkokerroin riippuen käytetystä asteikosta
s – asteikkokerroin riippuen käytetystä asteikosta
d – pysyvän sisennyksen syvyys verrattuna pieneen kuormitukseen, mm
Vickersin kovuuskoe
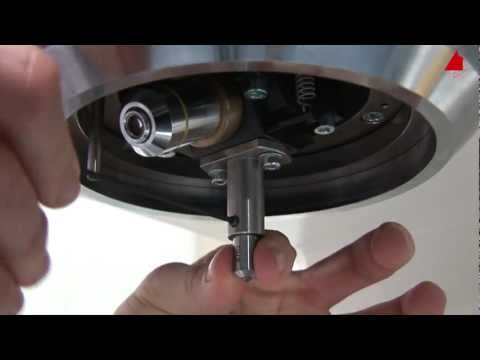
Vickersin kovuuskoe
kolmas tapa materiaalin kovuuden mittaamiseen on Vickersin testi. Tämä sopii erityisesti pehmeämmille materiaaleille, jotka eivät tarvitse suuria kuormia. Pehmeillä materiaaleilla Vickers-menetelmä tarjoaa paremman tarkkuuden.
myös kovuusarvon laskeminen on helpompaa, sillä Vickers käyttää samaa timanttisisustinta kaikissa materiaaleissa. Näin ollen kaavan säätäminen ei ole välttämätöntä.
toinen tärkeä ominaisuus on suurennuslasin käyttö, jolloin voidaan testata alueita, joilla on tietty mikrorakenne.
ensin testaajan on asetettava osa koneeseen ja käytettävä mikroskooppia sopivan korkeuden löytämiseksi. Sitten kuvien avulla määritetään oikea paikka.
timantin sisennys on nelisivuisen pyramidin muotoinen. Kosketettuaan osaa kone saavuttaa pian ennalta määritetyn voima-arvon. Se pysyy samassa kuormassa tietyn ajan.
tämän jälkeen sisennyksen mittaaminen tapahtuu. Vickersin kovuusarvon laskemisessa käytetään seuraavaa kaavaa:
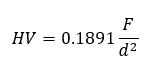
, jossa
F-voima, n
d-sisennyksen diagonaali, mm
Mohsin Kovuustesti
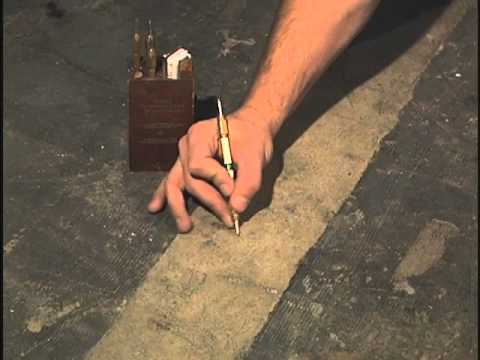
Mohsin kovuuskoe
saksalainen mineralogi Mohs laati ensin Mohsin kovuuskokeen materiaalien naarmuuntumiskovuuden mittaamiseksi. Tässä testissä materiaalia naarmutetaan vertailumateriaalilla, jonka kovuus on määritelty.
testimateriaalille annetaan numeerinen kovuusarvo testin tulosten perusteella. Mohsin kovuuskokeessa käytetään testin asteikkona 10 eri kovuista vertailumateriaalia.
pehmein käytetty materiaali on talkki (arvo=1) ja vaikein materiaali on timantti (arvo=10). Koska Mohsin asteikon viittauksissa ei ole asteittaista lisäystä, Mohsin asteikko ei ole tarkka ja on vain karkea kovuuden mittari.
nykyään nykyaikaiset raaputustestit suoritetaan Rockwell-timanttisisennyttimillä raaputtamalla testikappaletta tietyn pituisena valitun kuormitusarvon puristamana.
Skleroskooppitesti
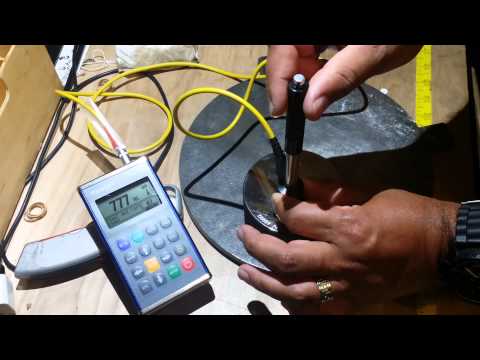
Rebound-Kovuustesti
skleroskooppi on Laite, jolla mitataan materiaalien rebound-eli dynaamista kovuutta. Asennus koostuu ontosta pystysuorasta lasiputkesta, joka on liitetty telineeseen. Tätä putkea pitkin timanttivasara pudotetaan testikappaleen päälle ja vasaran pomppiminen tallennetaan.
timanttivasara pudotetaan kiinteältä korkeudelta omalla painollaan. Joutuessaan kosketuksiin testikappaleen kanssa vasara kimpoaa takaisin. Tämä pomppu on korkeampi materiaaleille, joilla on suurempi kovuus.
pehmeälle metallille pomppu on pienempi, koska osa iskuenergiasta kuluu lommon luomiseen testipintaan. Lasiputkessa on kaltevuudet, joilla mitataan pomppukorkeutta. Rebound-kovuus mitataan shore-yksiköissä.