Tvrdosti je materiál je kvalitní, aby vydržely lokalizované deformace. To může být zvláště důležité při hledání vhodného materiálu pro prostředí, které obsahuje malé částice, které mohou vyvolat opotřebení materiálu. Měkké materiály trpí zářezy, zatímco tvrdé odolávají jakékoli změně tvaru.
tvrdost by měla být viděna v kontextu s jinými vlastnostmi materiálu, jako je pevnost, pružnost atd. Například mnoho tvrdých materiálů bývá křehkých, což omezuje jejich použití.
v tomto článku se blíže podíváme na to, jaká je tvrdost materiálu, jak se měří a jak porovnávat různé jednotky.
Co Je Tvrdost Materiálu?
tvrdost je měřítkem odolnosti materiálu vůči lokalizované trvalé deformaci. Trvalá deformace se také nazývá plastická deformace. Zatímco elastická deformace znamená, že materiál mění svůj tvar pouze během působení síly, výsledná plastická deformace znamená, že se materiál nevrátí do svého původního tvaru.
některé materiály jsou přirozeně tvrdé. Například wolfram je neuvěřitelně tvrdý kov, který se používá jako legující prvek v nástrojových ocelích. Tím je zajištěno, že tato skupina ocelí může odolat opotřebení i při vysokých teplotách během řezných operací.
slinutý karbid, který najde mnoho využití v fréz, také často zahrnuje wolfram. Tyto vyměnitelné bity řezného nástroje značně prodlužují životnost řezných nástrojů.
na druhé straně některé materiály, včetně kovů, jsou měkké do té míry, že je činí zbytečnými pro mnoho aplikací. Čisté zlato je tak měkké, že poškrábání nebo ohýbání nevyžaduje mnoho úsilí. Přidání dalších kovů, jako je stříbro, měď a hliník, je proto nezbytné pro zlepšení jeho tvrdosti.
u některých materiálů je tepelné zpracování možností indukovat větší tvrdost povrchu při zachování ostatních vlastností kovu v jeho jádru. Hřídele stroje často procházejí tímto procesem, aby byla zaručena delší životnost.
inženýr musí také zvážit poměr tvrdosti při vytváření konceptu návrhu produktu. Například při uložení ložiska a hřídele musí být ložisko měkčí, protože se snáze vyměňují. Při neustálém pohybu musí jedna část nosit a volba je na inženýrovi.
druhy tvrdosti
materiály se při různých typech zatížení chovají odlišně. Například kov, který může mít obrovský jednorázový dopad velmi dobře, nemusí při nepřetržitém zatížení působit stejně.
zkoušky tvrdosti musí být provedeny pro každý případ, aby bylo možné pro aplikaci provést dobře informovanou volbu.
tři typy tvrdosti jsou poškrábání, odskočení a tvrdost odsazení. Měření každého typu tvrdosti vyžaduje jinou sadu nástrojů. Stejný materiál bude mít také různé hodnoty tvrdosti pro každý z výše uvedených typů.
tvrdost odsazení
Tento typ tvrdosti označuje odolnost vůči trvalé deformaci při vystavení materiálu nepřetržitému zatížení.
tvrdost odsazení je to, na co inženýři a metalurgové obvykle odkazují, když mluví o tvrdosti. Měření jeho hodnoty je prvořadým zájmem, protože kontinuální zatížení je nejběžnější formou nakládání kovů.
tvrdost proti poškrábání
Tento typ tvrdosti označuje schopnost materiálu odolávat poškrábání na povrchu. Škrábance jsou úzké souvislé zářezy v horní vrstvě v důsledku kontaktu s ostrým, tvrdším materiálem.
testování poškrábání se také běžně používá pro křehké materiály, jako je keramika, protože nepodléhají významné plastické deformaci. Je důležité zvážit tvrdost poškrábání, protože některé materiálové aplikace jsou vysoce citlivé na bodování.
zvažte případ vložky válce motoru jako příklad. Poškrábání nebo bodování může probíhat z různých důvodů. Povrch vložky přichází do styku s různými kovy, jako jsou pístní kroužky, cizí částice v palivu nebo mazací olej. Někdy k tomu může přispět nesprávné sezení vložky.
brusné částice mohou způsobit škrábance, které v konečném důsledku snížit výkon motoru a dražší na údržbu, náhradní díly, a spotřeba paliva v dlouhodobém horizontu.
ve fázi návrhu správný výběr kovu zvažuje tvrdost materiálů, se kterými přijde do styku. Tvrdost vložky musí být větší než materiály, se kterými bude interagovat. To pomáhá odvrátit mnoho možných problémů.
odrazová nebo dynamická tvrdost
odrazová tvrdost má více společného s elastickou tvrdostí než tvrdost plastu. Materiál absorbuje energii při nárazu a vrací ji do vnitřku.
indenter je referenční materiál používaný pro zkoušení tvrdosti. Dynamická tvrdost je obvykle měřena tím, že upustí diamant-naklonil kladivo na zkušební kus a nahrávání kladivo odrazit po to udeří povrch.
čím blíže je výška k původní výšce pádu, tím vyšší je hodnota tvrdosti odrazu.
Získat vaše kovovýroba citace v sekundách
-
Citace v sekundách
-
Krátké dodací lhůty
-
Dodání Továrním
citace
Různé Tvrdosti Jednotky
jednotkou tvrdosti je N/mm2. Jednotka Pascal se tedy používá také pro tvrdost, ale tvrdost nesmí být zaměňována s tlakem.
různé typy tvrdosti diskutované výše mají různé stupnice měření. V případě tvrdosti poškrábání, odsazení a odrazu se metody měření liší (např. Brinell, Rockwell, Knoop, Leeb a Meyer). Jako jednotky jsou odvozeny z těchto měření metodami, které nejsou vhodné pro přímé srovnání.
vždy však můžete použít konverzní tabulku pro porovnání hodnot Rockwell (B & C), Vickers a Brinell. Tabulky, jako jsou tyto, nejsou 100% přesné, ale dávají dobrou indikaci.
Brinell Hardness | Rockwell | Rockwell | Vickers | N/mm² |
HB | HRC | HRB | HV | |
469 | 50 | 117 | 505 | |
468 | 49 | 117 | 497 | |
456 | 48 | 116 | 490 | 1569 |
445 | 47 | 115 | 474 | 1520 |
430 | 46 | 115 | 458 | 1471 |
419 | 45 | 114 | 448 | 1447 |
415 | 44 | 114 | 438 | 1422 |
402 | 43 | 114 | 424 | 1390 |
388 | 42 | 113 | 406 | 1363 |
375 | 41 | 112 | 393 | 1314 |
373 | 40 | 111 | 388 | 1265 |
360 | 39 | 111 | 376 | 1236 |
348 | 38 | 110 | 361 | 1187 |
341 | 37 | 109 | 351 | 1157 |
331 | 36 | 109 | 342 | 1118 |
322 | 35 | 108 | 332 | 1089 |
314 | 34 | 108 | 320 | 1049 |
308 | 33 | 107 | 311 | 1035 |
300 | 32 | 107 | 303 | 1020 |
290 | 31 | 106 | 292 | 990 |
277 | 30 | 105 | 285 | 971 |
271 | 29 | 104 | 277 | 941 |
264 | 28 | 103 | 271 | 892 |
262 | 27 | 103 | 262 | 880 |
255 | 26 | 102 | 258 | 870 |
250 | 25 | 101 | 255 | 853 |
245 | 24 | 100 | 252 | 838 |
240 | 23 | 100 | 247 | 824 |
233 | 22 | 99 | 241 | 794 |
229 | 21 | 98 | 235 | 775 |
223 | 20 | 97 | 227 | 755 |
216 | 19 | 96 | 222 | 716 |
212 | 18 | 95 | 218 | 706 |
208 | 17 | 95 | 210 | 696 |
203 | 16 | 94 | 201 | 680 |
199 | 15 | 93 | 199 | 667 |
191 | 14 | 92 | 197 | 657 |
190 | 13 | 92 | 186 | 648 |
186 | 12 | 91 | 184 | 637 |
183 | 11 | 90 | 183 | 617 |
180 | 10 | 89 | 180 | 608 |
175 | 9 | 88 | 178 | 685 |
170 | 7 | 87 | 175 | 559 |
167 | 6 | 86 | 172 | 555 |
166 | 5 | 86 | 168 | 549 |
163 | 4 | 85 | 162 | 539 |
160 | 3 | 84 | 160 | 535 |
156 | 2 | 83 | 158 | 530 |
154 | 1 | 82 | 152 | 515 |
149 | 81 | 149 | 500 |
ve všech těchto stupnicích bude mít tvrdý materiál vyšší číslo tvrdosti.
běžně používané jednotky pro měření tvrdosti jsou:
- Tvrdost podle Brinella Číslo (HB)
- tvrdosti dle Vickerse číslo (HV)
- Rockwell tvrdost číslo (HRA, HRB, HRC, atd.)
- Leeb tvrdost hodnota (HLD, HLS, HLE, atd.)
Měření Tvrdosti
různé typy tvrdosti se měří pomocí různých testovacích metod. Samozřejmostí mezi všemi metodami je použití odsazení k vytvoření odsazení na povrchu zkušebního kusu. Odsazení poskytuje hmatatelné znázornění tvrdosti materiálů a lze jej snadno měřit a replikovat.
tvrdší materiály budou mít mělké zářezy a měkčí materiály budou mít hlubší zářezy.
Zkouška Tvrdosti podle Brinella

Zkouška Tvrdosti podle Brinella
podle Brinella zkouška byla jednou z prvních široce uznávané zkoušky tvrdosti pro odsazení tvrdost měření. V brinellově zkoušce se ocelová koule o průměru 10 mm používá jako indenter k vytvoření dojmu na zkušebním kusu pro výpočet jeho čísla tvrdosti Brinell.
míč je držen na místě po předem stanovenou dobu, obvykle 30 sekund, a na míč je aplikována síla. Tato síla se bude lišit v závislosti na měřeném zkušebním kovu.
standardní zatížení je 3000 kg, ale u měkčích kovů může být sníženo na 500 kg. U tvrdších kovů může být použita kulička z karbidu wolframu, aby se zabránilo zkreslení koule. Jednotka tvrdosti HB (nebo HBN) bude změněna na HBW v případě wolframu, aby oznámila jeho použití (Wolfram=Wolfram v němčině/švédštině).
při odstranění indentoru je dent pozorován mikroskopem s nízkým výkonem a velikost se vypočítá tak, že se vezme průměr měření v pravém úhlu.
po dokončení Brinellovy zkoušky se číslo tvrdosti vypočítá následovně:
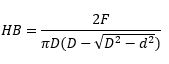
, kde
F – síla, N,
D – indenter průměr, mm
d – odsazení průměr, mm
Rockwell Zkouška Tvrdosti

Rockwell Zkouška Tvrdosti
Rockwell zkouška tvrdosti je nejvíce běžně používaná metoda pro odsazení tvrdost měření. Hodnota tvrdosti Rockwell je doprovázena použitou stupnicí.
V závislosti na zkoušeném materiálu musí být zvolena vhodná stupnice. Tato stupnice tvrdosti poskytuje informace o typu použité kombinace mezi zatížením.
K dispozici je celkem 30 stupnic. Díky tomu je Rockwell měřítkovým testem pro měření tvrdosti široké škály materiálů. Jsou možná i měření tvrdosti keramického a kompozitního materiálu. Nejčastěji používané váhy jsou “ B “ A „C“.
V Rockwell zkouška tvrdosti, před použitím testování zatížení, malý, menší zatížení sedadla indenter do zkušebního kusu a odstranit efekt jakékoliv nerovnosti povrchu. To poskytuje lepší přesnost.
pak podobně jako u Brinellova testu se indenter používá k vytvoření dojmu na materiál použitím testovacího zatížení známého také jako hlavní zatížení. Dojem se pak měří pro stanovení tvrdosti. K zaznamenání deformace se používá číselník.
pro výpočet hodnoty tvrdosti se uvažuje čistý nárůst rozměru zubu (mezi aplikací malého a velkého zatížení).
je nutné zadat rychlost načítání. U měkkých kovů mohou různé rychlosti aplikace zatížení způsobit znatelný rozdíl v konečné hodnotě. Je důležité pečlivě sledovat, zda je rychlost načítání podle standardu.
vzorec pro tvrdost Rockwell je:
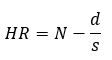
, kde
N – faktor měřítka v závislosti na měřítku,
s – faktor měřítka v závislosti na měřítku,
d – hloubka trvalého vtisku ve srovnání s menší zatížení, mm
Vickerse Zkouška Tvrdosti
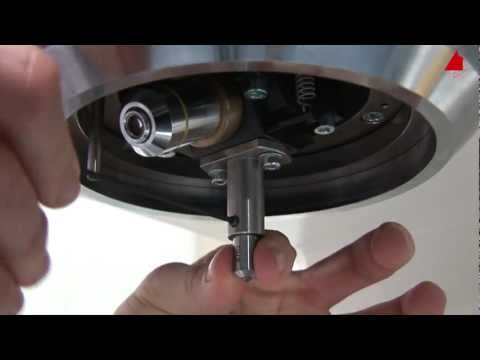
Vickerse Zkouška Tvrdosti
třetí způsob, jak pro měření tvrdost materiálu je pomocí Vickers test. To je zvláště vhodné pro měkčí materiály, které nepotřebují vysoké zatížení. U měkkých materiálů poskytuje metoda Vickers lepší přesnost.
také výpočet hodnoty tvrdosti je jednodušší, protože Vickers používá stejné diamantové indenter pro všechny materiály. Ladění vzorce tedy není nutné.
Další důležitou vlastností je použití lupy, což umožňuje testovat oblasti se specifickou mikrostrukturou.
nejprve musí tester umístit díl na stroj a pomocí mikroskopu najít vhodnou výšku. Poté se pomocí obrázků určí správné místo.
diamant indenter má tvar čtyřstranné pyramidy. Po dotyku součásti stroj brzy dosáhne předem stanovené hodnoty síly. Po určitou dobu zůstává na stejném zatížení.
poté se provede měření odsazení. Výpočet hodnoty tvrdosti Vickers používá následující vzorec:
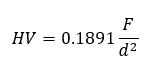
, kde
F – síla, N,
d – odsazení diagonální, mm
Tvrdost podle Mohse Test
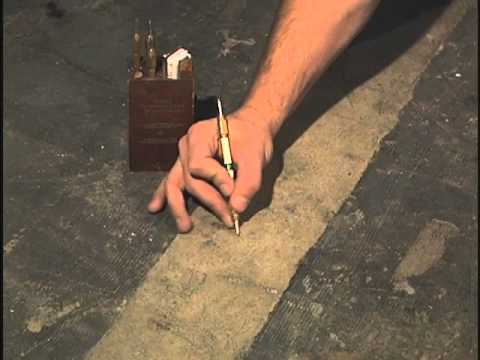
Tvrdost podle MOHSE Test
německý mineralog Mohs první vymyslel Mohs tvrdost test pro měření nuly tvrdosti materiálů. Při této zkoušce je materiál poškrábán referenčním materiálem, který má definovanou tvrdost.
na základě výsledků zkoušky je zkoušenému materiálu přiřazena číselná hodnota tvrdosti. Mohsova zkouška tvrdosti používá jako měřítko pro zkoušku 10 referenčních materiálů s různou tvrdostí.
nejměkčím materiálem je mastek (hodnota=1) a nejtvrdším materiálem je diamant (hodnota=10). Vzhledem k tomu, že odkazy použité pro Mohsovu stupnici nemají odstupňované zvýšení, Mohsova stupnice postrádá přesnost a je pouze hrubým měřítkem tvrdosti.
dnes se Moderní stírací testy provádějí pomocí diamantových odsazovačů Rockwell poškrábáním zkušebního kusu na určitou délku stisknutou vybranou hodnotou zatížení.
Scleroscope Test
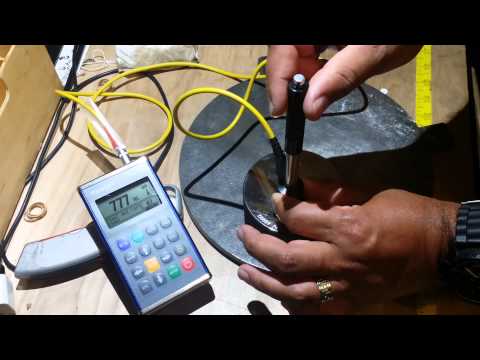
Oživení Zkouška Tvrdosti
scleroscope je zařízení používané k měření odrazu nebo dynamické tvrdosti materiálů. Instalace se skládá z duté svislé skleněné trubice připojené ke stojanu. Prostřednictvím této trubice se na zkušební kus spadne diamantové kladivo a zaznamená se odraz kladiva.
diamantové kladivo je upuštěno z pevné výšky pod vlastní hmotností. Při kontaktu se zkušebním kusem se kladivo odrazí zpět. Tento odraz bude vyšší u materiálů s vyšší tvrdostí.
odraz bude nižší pro měkký kov, protože část energie nárazu bude vyčerpána při vytváření zubu na zkušební ploše. Skleněná trubice má přechody pro měření výšky odrazu. Tvrdost odrazu se měří v jednotkách shore.